ENVIRONMENTAL POLICY
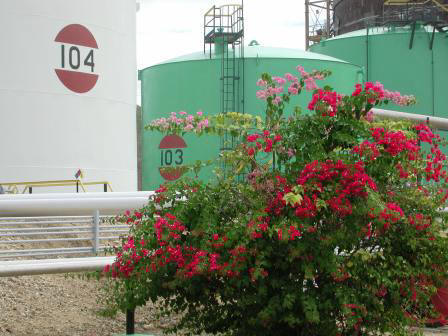 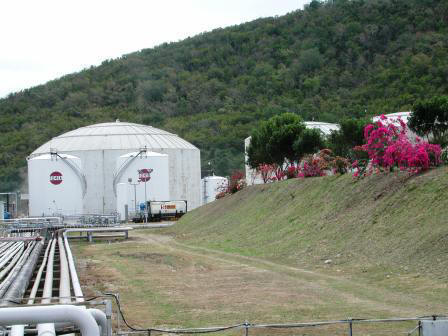 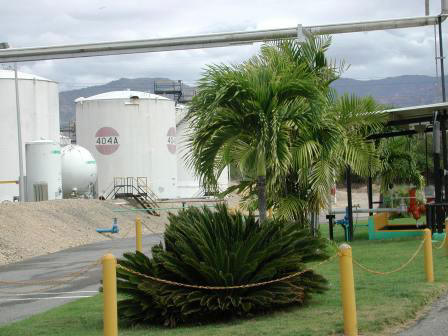
 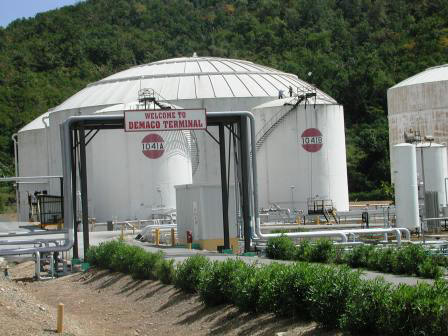 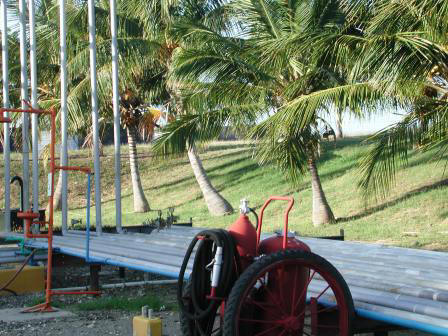
In today's
world, environmental concerns are everyone's business. At Demaco, we have always been sensitive to the well-being
of the community at large. That is why our safety
procedures for receiving, storing, and dispatching meet
or exceed the most stringent in the industry. It's smart
to be environmentally sensitive. We live here too! We
are careful because we truly care about our community,
its people, and our environment.
ENVIRONMENTAL COMPLIANCE:
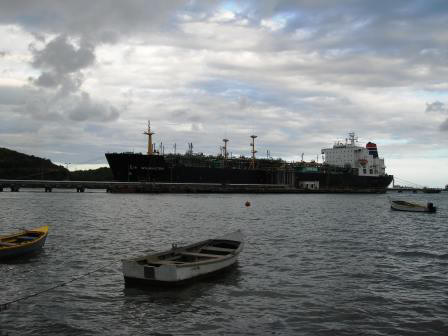 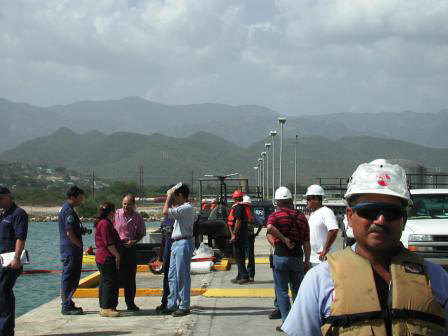
Clean Water Act(40 CFR 112)
Oil Pollution Prevention(SPCC). Demaco is responsible
for properly instructing its personnel in the operation
and maintenance of equipment to prevent the discharges
of oil and applicable pollution control laws, rules and
regulations. Demaco conducts spill prevention briefings
to assure adequate understanding of the SPCC Plan for
this facility.
Clean Water Act(40 CFR 125.104)
Best management practices associated with NPDES.
Discharges that use, manufacture, store, handle, or
discharge any toxic pollutants or hazardous pollutants
that could result in significant amounts of pollutants
reaching the waters of the U.S.
Resource Conservation and Recovery Act(RCRA)(40 CFR
264.16)
Hazardous waste management procedures. Ensures that
facility personnel are able to respond effectively to
emergencies by familiarizing them with emergency
procedures, emergency equipment, and emergency systems.
Oil Pollution Act(40 CFR 120.20)
Demaco is a Terminal facility regulated under 40 CFR
Part 112.20, which covers potential threats of substantial harm to
the environment through discharge of oil or hazardous
substances on navigable waters or adjoining shorelines.
Demaco is required to prepare and submit facility-specific
response plans to EPA in accordance with Appendix F of
40 CFR Part 112.
In
order to operate a chemicals terminal, Demaco must have
air permits for its storage tanks, fire pumps, and
emergency generators. We fully comply with these
requirements. Operation of the dock facilities is
regulated by the USCG. We have an approved USCG OPA
plan.
Special
points of Interests:
-
Demaco has submitted OPA plans both to the EPA and
USCG.
-
Demaco has submitted an SPCC Plan.
-
Demaco has submitted a BMP.
-
Demaco trains its personnel on a yearly basis on
these requirements.
VESSEL UNLOADING:
 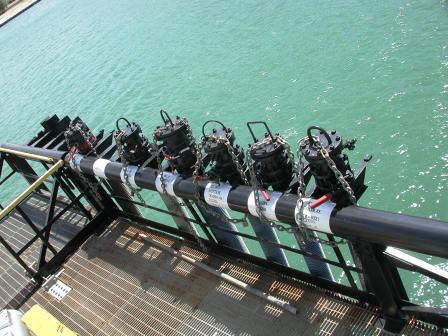 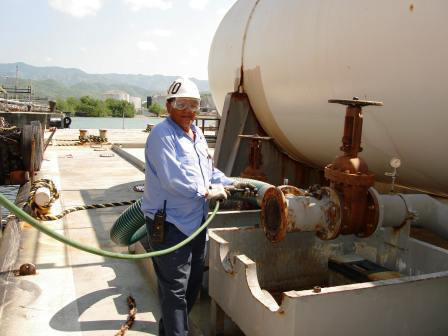
Quality, Safety and Health Observations
Unloading
vessels requires that employees be knowledgeable,
trained, and certified. Many parties monitor our
operations: the
US coast guard, OSHA, our clients, and you, the
end-user. Therefore, we concentrate on ensuring that
our work is performed correctly the first time. This job
cannot be done without check lists or written instructions, no
matter how many times performed previously. The
supervisor prepares a 14 page written procedure to
provide guidance on what to do from beginning to end.
These procedures cover all contingencies including, for
example, product spills into ocean
water, fires, personal injuries, product contamination with sea water,
etc. We must be prepared for all these possibilities.
Quality Assurance
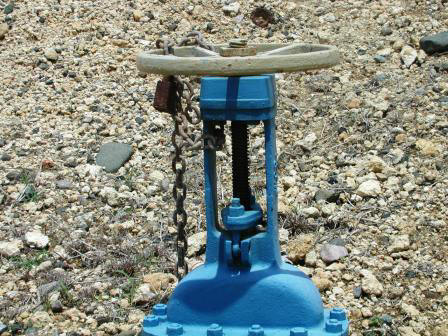 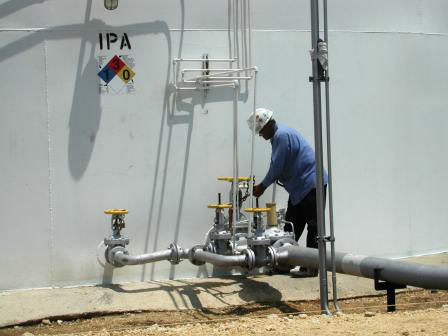 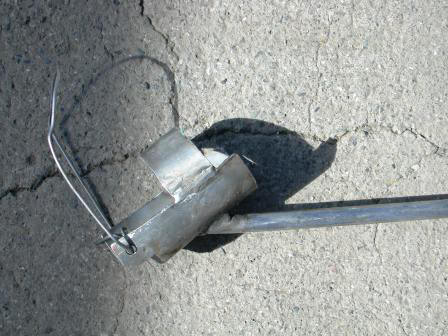
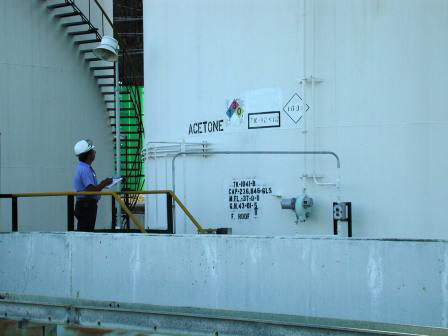 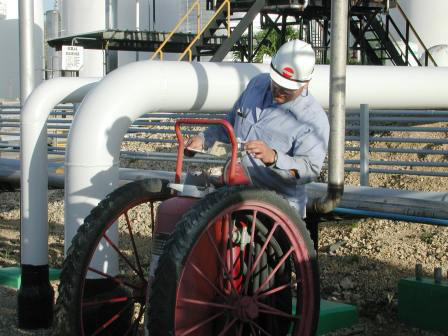 
Many products handled at our Terminal are used by
the pharmaceutical and food-processing
industries. Due care in the handling of these products
must be observed by all employees. How do we assure our
clients that we care about and observe quality?
- Pipeline Cleaning:
Multi-product pipelines must be clean prior to
transferring product through them. A record is kept.
- Product
Identification: All products aboard the vessel are
positively identified.
- Product Sampling:
All products shall be sampled. Unloading may not
take place until positive results are received from
the laboratory.
- Sample Taking:
Clean, sanitized instruments are used.
- Lot Numbers: A new
lot number is assigned by our client.
- Rejected product:
Client is notified. Unloading may not take place.
- Flushings: Prior
to transferring a product to the receiving tank, the
pipeline is flushed clean into a cargo tank.
- Security: Valves
are padlocked to deter tampering.
- Nitrogen Use:
Nitrogen (not air) is used to empty hoses and
pipelines into receiving tank to prevent fire
hazards and contamination of the product.
- Alcohol/drug
abuse: Strictly prohibited. Personnel must be alert
at all times.
Cargo Tank Loading:
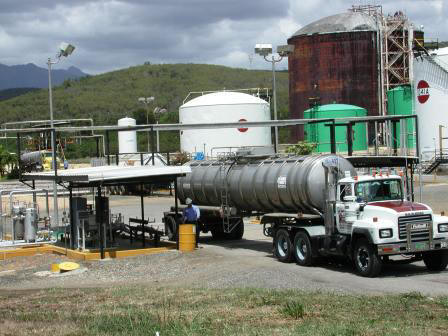 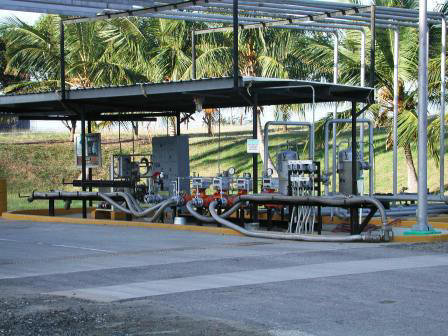 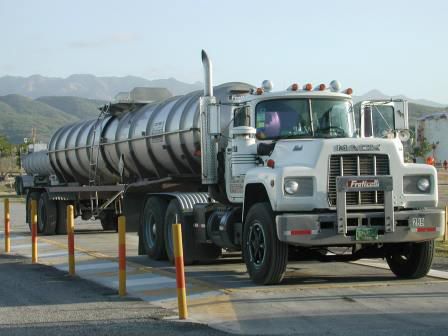
Cargo Tank Selection
and Inspection
Our client selects cargo tanks to transport their
products through Puerto Rico's highways. These vehicles
must comply with strict federal regulations. The
compatibility of the material of construction of the
tank with the product to be loaded is one of the most
important aspects to consider when selecting cargo
tanks. Upon arrival at the Terminal we conduct a
rigorous inspection of each cargo tank. There are five
inspections that each tank must have undergone prior to
being sent to us for loading: leakage, thickness, visual
external, visual internal, and pressure. We are not
responsible for conducting these inspections, but we are
responsible for ensuring that they have been performed.
Each inspection date is entered in Section 1A of the
inspection form. The material of construction is checked
next. What would happen if we load a product in a
non-compatible tank? An explosion, disintegration or
product contamination could occur. The maximum loading
weight to be loaded is also checked. If you ask for
7,000 gallons of a product and receive 6,000 gallons
instead, it is because we can not exceed the maximum
loading weight as stated in the cargo tank's
specification plate. Severe fines are imposed if we
surpass the maximum loading weight.
Up
ALL RIGHTS
RESERVED @ DEMACO CORP. 2022 |